Our team is pleased to report the improvements we’ve made to our component manufacturing services since integrating Lean manufacturing principles.
Leech Industries began our Lean manufacturing journey for three reasons:
- To exceed customer expectations: Whether they’re operating in aerospace, defense, or automotive, there is always an expectation that we are maximizing our efficiency and keeping our costs competitive.
- To remain competitive: We aim to be a top supplier, serving our customers to the best of our ability and outperforming our competitors. To do this, it’s essential that we keep our costs down and quality up, whether it’s through consolidating our workspaces, removing wasteful steps, or investing in cutting-edge equipment.
- To do right by the community: Inefficiency and waste don’t just impact our bottom line; they yield negative impacts on an environmental and global scale.
Let’s dive into Leech’s Lean journey, the steps we’ve taken to hone our processes and how our customers can benefit when they partner with a Lean manufacturer.
Steps We’ve Taken to Make Our Shop More Lean
Leech Industries held a Kaizen event with one of our customers, during which we identified waste within our processes for different part numbers. By monitoring current processes, searching for extra movement, working out defects, and reducing costs, we can establish goals to set our team up for success in our Lean manufacturing journey.
Here are just a handful of steps our team has taken in the last year:
Consolidating Our CNC Operations
In Q4 of 2023, a handful of our team members evaluated our waste and processes from a high-level Lean perspective. They assessed the movement of products back and forth between two buildings, investigating micro issues like the number of physical steps between locations to reach a macro solution of reducing wasted time. This led to consolidating our CNC operations under one roof to minimize steps and maximize efficiency. Further, the time identified opportunities to create CNC cells to allow one operator/multiple machine operation.
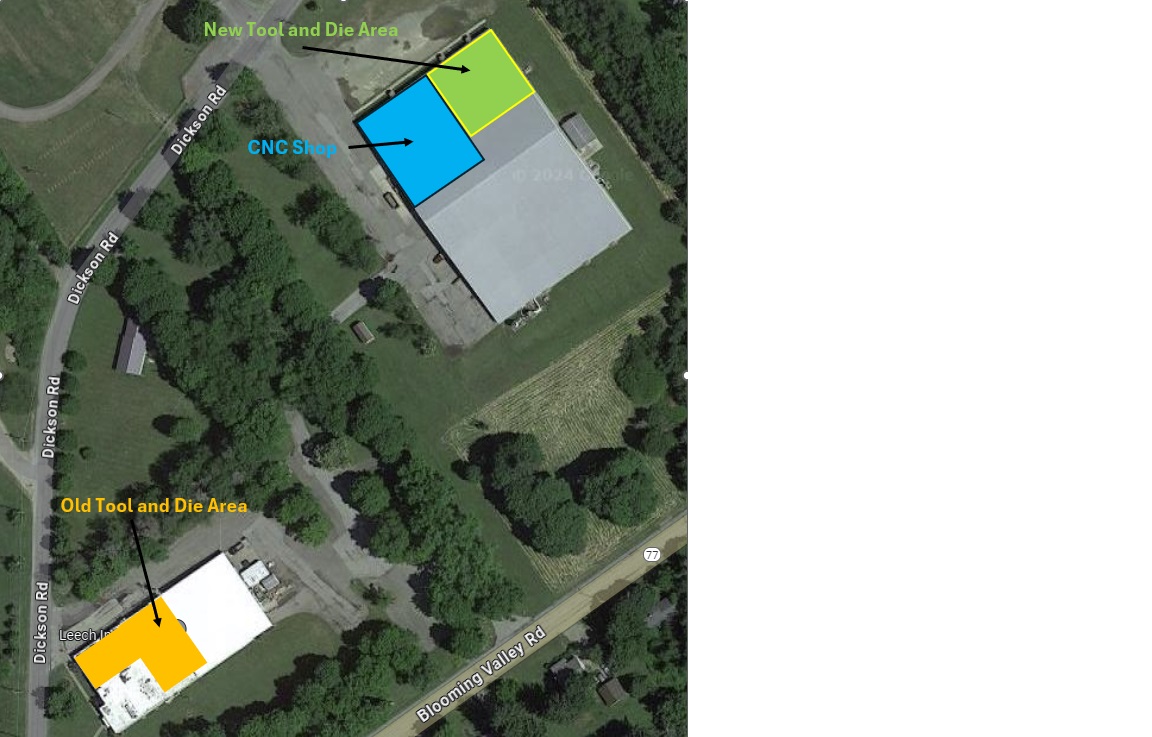
CNC shop used to be around 700 steps, now it’s about 70!
Reconfiguring Our Commodity Shops
Our team experienced something similar with commodity shops in our facilities. We had two shops separated by a central processing area. By relaying out that central processing area, thus reducing floor space, our team could cut out steps that added unnecessary time to our commodity operations.
How Our Customers Benefit from Working with a Lean Shop
The beauty of working with a Lean shop is that you don’t have to deal with any additional legwork on your end. Our teams handle the process improvements so our customers reap the following benefits:
Cost Savings
Streamlining our processes and reducing waste allow us to offer our customers more competitive prices. This, in turn, helps our customers reduce the cost of their end products so they can continue offering competitive rates to their customers.
Reduced Lead Times
By adopting Lean principles, the Leech team has sufficiently cut down on lead times.
Improved Quality and Repeatability
To become the leanest shop we can be, our teams have evaluated every one of our processes with rigorous documentation for predictability and repeatability. As a result, we can guarantee that we are operating consistently, efficiently, and with quality as a priority so our customers receive the same results every time.
Greater Agility and Less Risk
By operating Lean and green, the Leech Industries team can react more strategically and agilely when opportunities arise. Whether it is responding to increased demand, a design change or bringing a new product into production, Lean allows Leech to respond quickly and effectively.
Ready to get started? Request a quote from Leech Industries to reap the benefits of partnering with a Lean shop.
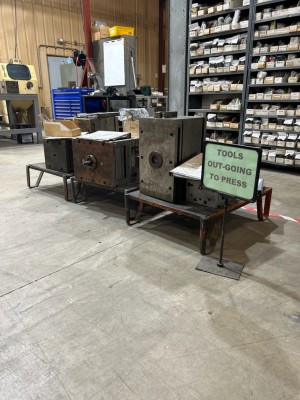
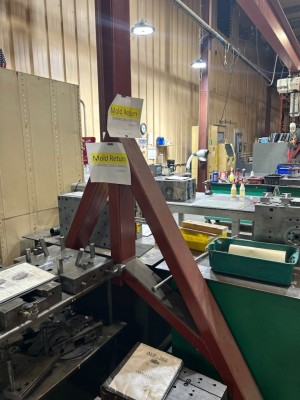