Sometimes customers approach us with projects that involve complex machining and intricate assemblies – such as the “NASA Project” we recently highlighted on the blog. Other times, they approach our team with pieces that don’t require super-tight tolerances or strict quality control protocols but that present their own unique challenges.
The Leech team played a critical role in the manufacturing of ratchets for one of our customers in the agricultural industry. For those unfamiliar with this sector, ratchets ensure high-tensile fencing remains under proper tension during installation.
This tool is not particularly complex and doesn’t require the stringent quality requirements we’re used to meeting for our aerospace or medical customers. However, our client faced a significant hurdle: an outdated, oversized, defunct mold inherited from another manufacturer. This mold not only exceeded the capacity of our machinery but also jeopardized production efficiency and part quality. In addition, we needed to think outside the box to meet the customer’s tight budget constraints.
We knew this project wouldn’t be easy but our team did what they do best: work creatively, critically, and collaboratively to exceed our customers’ expectations.
We’ll dive into the challenges the Leech Industries team faced with this project and the solutions we offered to deliver speed and cost-effectiveness.
How Our Tool and Die Shop Handled Our Customer’s Unique Challenges
The Challenge: An Extremely Oversized Mold
When the Leech Industries team got our hands on this mold, we noticed that it was unnecessarily big for the part it was making. We would need a much larger machine just to fit the mold, yet we wouldn’t need all the capacity this machine offered in terms of shot size. Overall, the piece was inefficient and not size-appropriate.
Our Solution: Transforming This Legacy Mold
To address this challenge, we cut this oversized mold in half, transforming it from a two-cavity mold to a single-cavity mold. This alteration allowed us to fit the mold into a more appropriately sized machine, boosting efficiency significantly. Our team rose to the occasion, refurbishing the mold and implementing necessary modifications to ensure seamless functionality.
The Challenge: Efficiency as a Pain Point
Even though refurbishing this customer’s mold helped improve productivity, the machine we needed to run this mold on was the oldest one in our facilities at the time. Since we knew we would be retiring this equipment soon, we knew we’d need to move the mold to one of our newer, more efficient machines.
Our Solution: Decreasing Cycle Time
Our team built a custom mold for our customer, that was designed to the press we knew we would use, resulting in a total reset for this piece. By transitioning to a modern press equipped with the upgraded mold, we achieved remarkable results. The original 60-second cycle time was slashed to 17 seconds, marking a substantial 43-second decrease. This exponential increase in efficiency optimized production throughput and significantly lowered manufacturing costs.
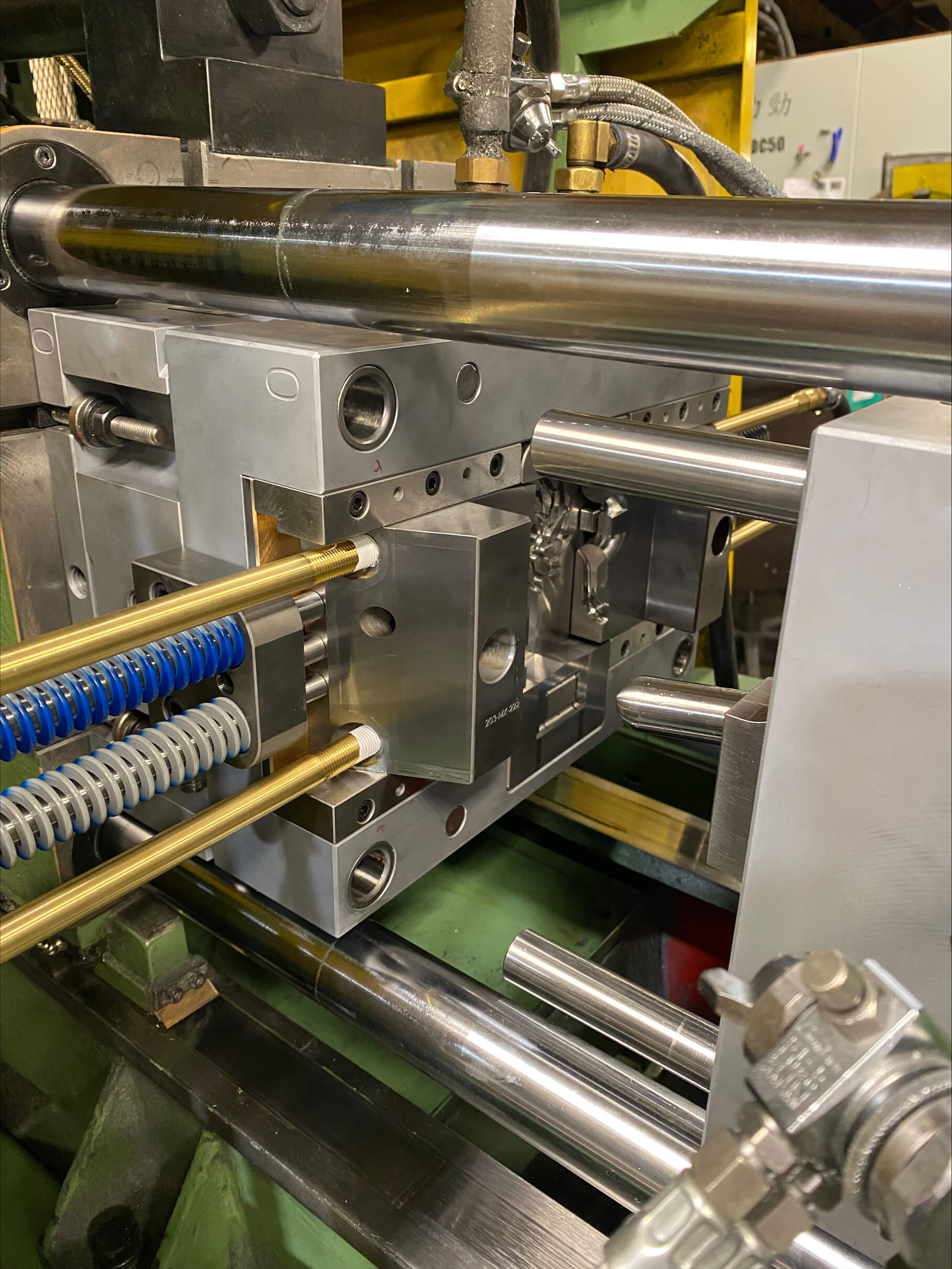
The Benefits of Tailored Contract Manufacturing Services from Leech Industries
In the instance of this ratchet mold and beyond, our approach to mold refurbishment and optimization is driven by versatility and client-centricity. We welcome clients with old, worn-out molds, offering tailored solutions to meet their diverse needs. Whether it's salvaging end-of-life molds or enhancing existing ones for improved quality and efficiency, our team stands ready to deliver innovative solutions.
Collaborating with Leech Industries yields a multitude of benefits for our customers:
Stable Pricing
Through strategic interventions and process optimizations, we enable our customers to maintain stable pricing despite evolving market dynamics. By enhancing efficiency and minimizing production costs, we ensure competitive pricing without compromising on quality.
Greater Efficiency
By implementing cutting-edge technologies and refurbishing outdated molds, our team empowers our customers to achieve faster turnaround times, enhancing their operational agility and market responsiveness.
One-Stop Solutions
The transformation of our customer’s ratchet manufacturing process is a testament to the culture of innovation and collaboration that guides Leech’s one-stop solutions. Being a molder in addition to a tool and die shop allows us to see production all the way through, from meeting quality standards to providing repairs as needed.
At Leech Industries, we are committed to delivering excellence and driving value for our customers from prototype to production and across industries. Partner with our dynamic team today!
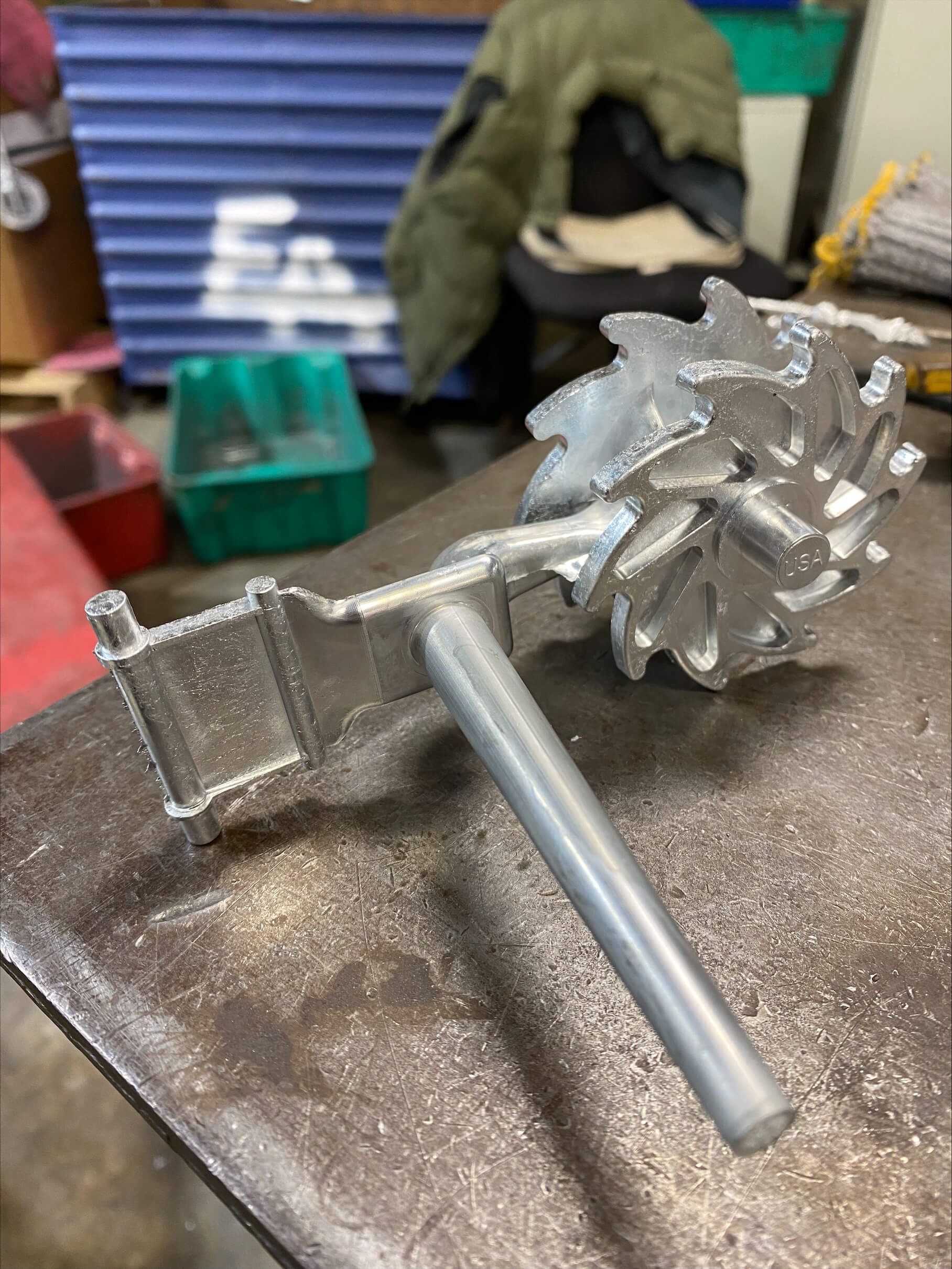