Leech Industries has plenty of experience working with customers to develop new products from the initial design stage to testing, all the way through full production. Thanks to our design and engineering team’s support and our production team’s invaluable experience, we can turn customers’ concepts into high-quality parts and test them to ensure optimal performance.
Our prototyping manufacturing services allow us to work efficiently as a one-stop shop, providing first runs and a range of services under one roof. If you’d like to find out more about how Leech Industries’ comprehensive prototype solutions can serve your individual needs, don’t hesitate to contact us.
The Value-Add of Leech’s Prototype Manufacturing Services
At Leech Industries, we actively seek out new challenges. That’s why we’re eager to work with manufacturers in the early prototyping stages to turn their concepts into tangible products.
Our customers benefit from working with the same shop for their prototype and production needs. To streamline production or optimize efficiency, Leech adds value in the following ways:
Cost-Effective Prototyping
Our expertise in production manufacturing allows us to build prototypes slightly differently than we would eventually develop full production runs. We can cut costs by utilizing less costly materials that will yield similar results during the prototyping phase.
For instance, when we build plastic injection molds that must withstand heavy-duty work over multiple years, we need to use the hardest materials to ensure the tool can handle significant wear. When we’re creating prototype molds, however, longevity is much less important, so we may opt to use lower-cost materials that provide similar results during testing.
This simple change is just one of the many ways we can reduce customer costs. Depending on the design, we may even be able to incorporate some configurable options to trial different geometries, materials, or assembly methods. Regardless, our prototyping capabilities are strengthened by our understanding of what is critical (and what is not). We ask our customers the right questions during this stage to ensure we provide precisely what they want – even when they aren’t entirely sure yet.
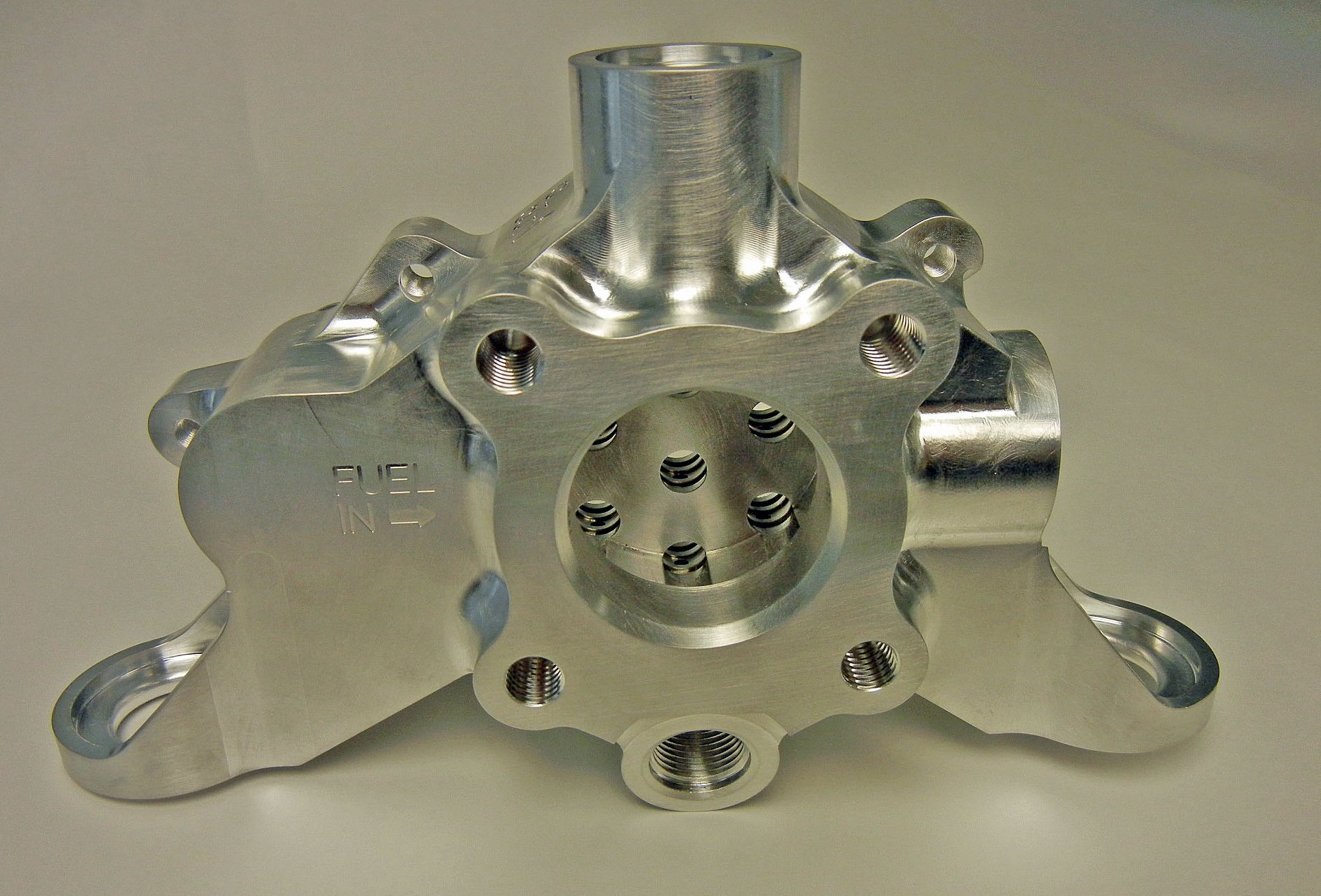
In-House Testing
Our team handles the following testing in our state-of-the-art facilities:
- Dimensional testing
- Tool functionality testing for our commodities market (injection molding, zinc die casting and stamping)
- Quality inspection
Thanks to our tool-building prowess, we’ve been able to add testing services as needed. For instance, we recently had a project that required pull testing on multiple samples. Rather than pausing the production run to outsource this testing, we outfitted a press with all the necessary equipment to perform this test. We even earned the necessary certification to handle in-house pull testing. Another time, a customer wanted parts inspected in a different way partway through production, so we built gauges to perform this new testing method. Here at Leech, we’re willing to go to significant lengths to surpass customer expectations and satisfy their testing needs and requirements.
For additional testing services, Leech Industries has a network of quality vendors and inspection labs that facilitate any specialized testing we do not handle in-house.
Efficiency in Production
When our team facilitates the prototyping stage, we become better equipped to handle production. Because we already know how to make the product – what material to use, where to order material from and what vendor will handle outside services and inspection – we can produce parts much more efficiently, having already done the legwork on the prototypes. This reduces (and often eliminates) back and forth dialogues with customers, as we already know what they need and how we can achieve this.
Quality Considerations
Quality is paramount at Leech Industries from prototype to full production. When our team builds prototypes, we sometimes reveal a quality-sensitive dimension on the part. If we are aware of intricate dimensions or complex geometries as early as the prototyping stage, we can act quickly and think creatively about how to handle it. Because we already determined how to handle all critical features, the chances of slow-downs or complications during machining are minimal to nonexistent.
Engineering Mindset
At Leech, our estimators are engineers at heart. They take on tasks from an engineering standpoint, seeing projects through genesis to delivery while leveraging their in-depth industry knowledge. The engineering team is happy to provide DFM support to customers to yield quality prototypes that will become exceptional production components.
Single Point of Contact from Prototype to Production
Vetting and building relationships with both a prototype shop and a production facility can be time-consuming. In addition, working with multiple shops for prototyping and production may result in knowledge loss. Trusting one shop with all services ensures the people handling your prototyping needs will also be facilitating the full production run.
One-Stop Prototype Manufacturing Services
To summarize our prototype to production services: at Leech, we’re “in for a penny, in for a pound.” We will work closely with you to build a single prototype piece and we’ll continue to support you when you need 10,000 parts.
When you need high-quality prototypes that will eventually translate to full production runs, partner with Leech Industries for services you can trust. With a range of services and top-notch customer support, our team has the versatile solutions to readily exceed your expectations.
Request a quote to get started on your prototype batch – or to jump right into production.